Lost wax casting
Lost wax casting: a new service offered by Corsa 3d.
Corsa 3d – in order to complete its range of 3d printing services – has decided to include the production of wax masters for casting. With the installation of a System CPX 3500 lost wax 3d printer, you can get very precise waxes, suitable for the process of lost wax casting of details of very complex geometries in brass, bronze, aluminum, steel and precious alloys.
The majority of 3D printing technologies is direct, that is, it directly creates the finished object without the need for further steps: these include, for example, fused deposition modeling, stereolithography and many more.
There are, however, indirect methods of 3D printing, one of which is the so-called lost wax technique. Known also as lost wax casting or precision casting, lost wax casting provides for the creation of a duplicate or clone of an original mold, usually from a metal such as gold or silver.
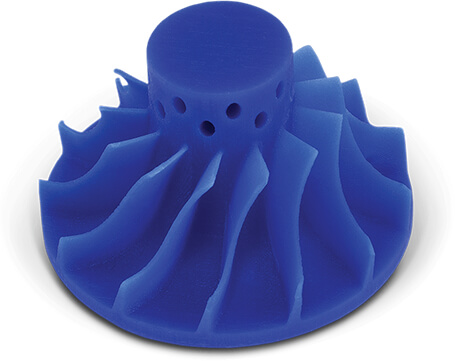
Lost wax casting:
some interesting facts on the origin and the use of this technique.
The lost wax casting technique has a rich history: it is a sculptural technique originally introduced during the Bronze Age and that over the centuries flourished considerably, especially in Greek and Roman art and in monumental sculpture. In Southern Israel, objects have been found, created by using the lost wax casting technique, dating back to 3700 BC. Over 5700 years have passed since then!
Lost wax casting is therefore a very old technique, that was later used even before 3D printers came on the scene. With this technique, you can create a mold from a prototype made with wax. Over the past few years, lost wax casting has become very popular in the world of jewelry and it is usually used to create prototypes of the master model that will then be mass-produced with traditional methods. It is a very useful method for producing a high amount of custom pieces, and it is particularly suitable for replicating very detailed projects quickly and precisely. Before the 3D printer, artisans used to transform these prototypes by hand, meticulously carving the details in a solid block of wax. Nevertheless, understandably, the technology of 3D printing has made the creation of a wax prototype easier and faster.
The lost wax technique is an established practice for producing equipment for the medical and aerospace industries and it is also used in foundries: the System CPX 3500 max professional lost wax 3d printer in fact guarantees an output that respects the requirements of precision and reliability and produces wax models that can be melted by any foundry.
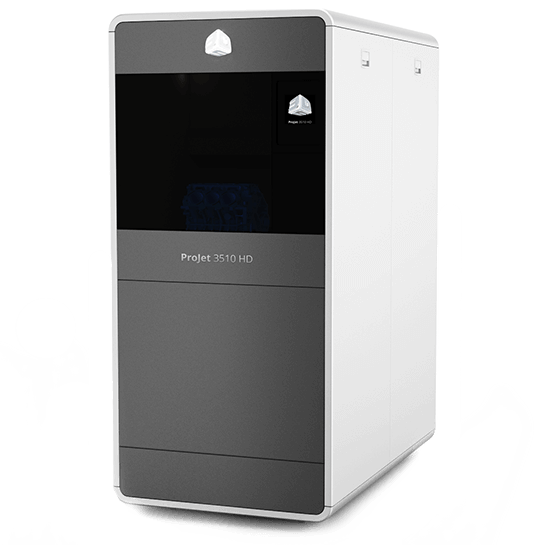
Lost wax processing: a simple but detailed explanation.
The essential steps of lost wax casting are, in particular, the following:
- Lost wax 3d master printing: this process replaces the injection process of wax in the specific mold;
- Casting shaft assembly: the models are assembled on a lost wax casting shaft;
- Creation of the ceramic shell: the whole shaft is immersed in a ceramic bath in order to create a shell that is resistant to melting temperatures. This bath is repeated several times with grains of different ceramic materials, from the finest in direct contact with the wax, to the coarsest at the exterior, until the required thickness is reached;
- Wax leakage (or lost wax 3d molds): once the ceramic shell is dried, preheating to melt the wax is executed, leaving the ceramic shell ready for the lost wax casting;
- Metal casting: after having annealed the shell at a high temperature, making it almost glassy, you can proceed to the process of metal casting by gravity;
- Breakage of the shell: subsequent to the cooling and solidification of the metal, you can break the shell and extract the cast;
- Deflashing: the raw details are separated from the lost wax casting with an angle grinder;
- Finishing: the details are polished, sandblasted and – if necessary – worked on the CNC and then sent out.
In conclusion, the advent of 3d printing in lost wax casting has made it possible – and makes it possible – not only to reduce the total costs of the process – one need only think of the elimination of the mold in which the wax is injected – but to also reduce the overall production time.
The CPX 3500 lost wax 3d printer makes it possible to print, thanks to the presence of support material soluble in isopropyl alcohol, complex geometries with important undercuts, limiting the cleaning time.
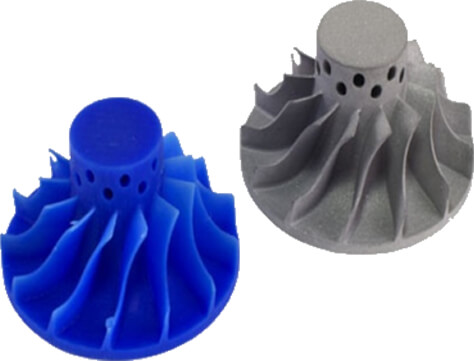
Lost wax casting process
Would You Like To Realise Your Project With Us?